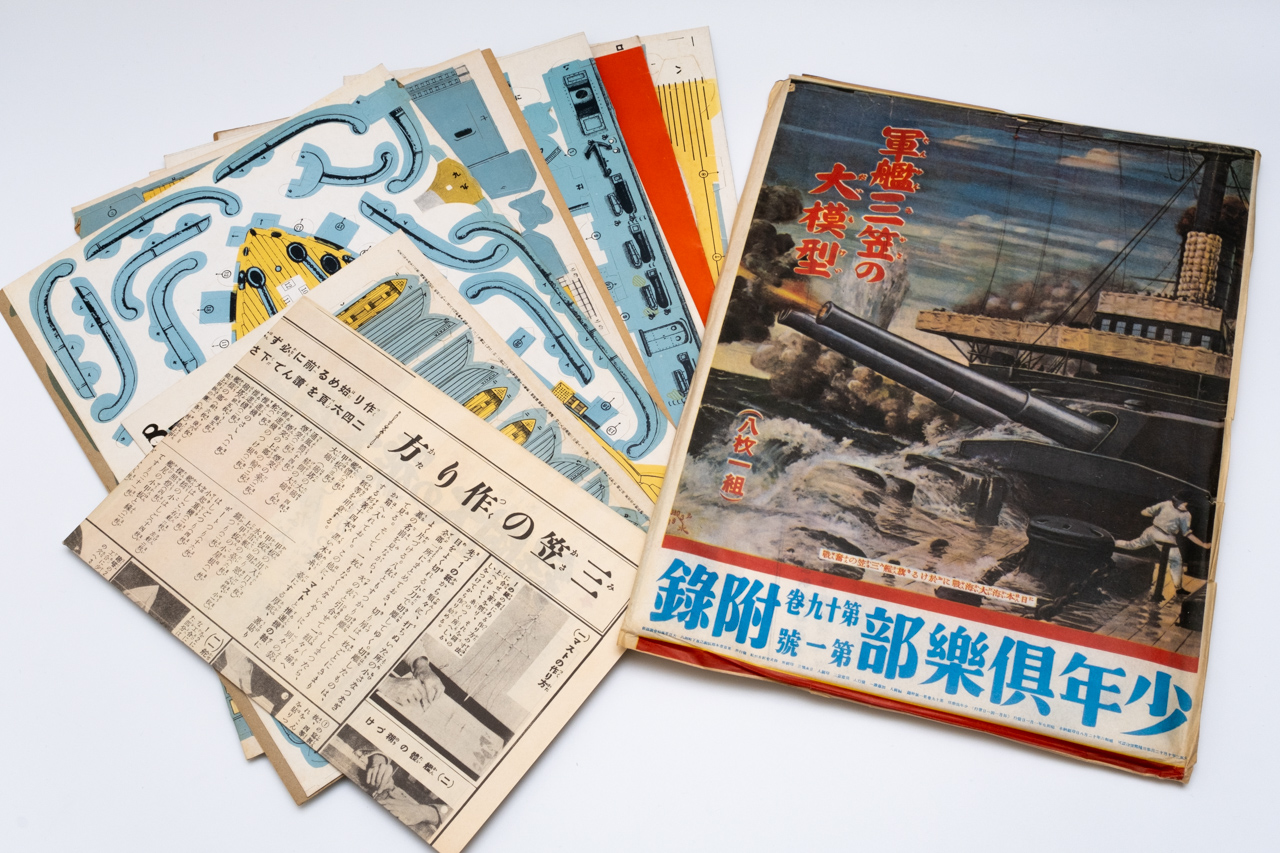
Tokyo Shiki, as the name suggests, is a paper container company. However, unlike typical paper container companies that make general boxes, we have mainly focused on die-cutting of printed materials, often referred to as ‘thin items’. Using molds, we perform tasks such as adding creases for folding, incorporating perforations, cutting out shapes, and punching holes in printed paper.
At first glance, it might seem like anyone with the machinery and molds could do it, but in reality, it requires extremely delicate skills that necessitate adjustments in the microscopic realm. Our company has inherited and refined these techniques for over 60 years.
In this series, we will extract content from our company’s internal training original texts and introduce information related to die-cutting, including its history and specialized terminology. We would be delighted if readers could gain even a slight interest in die-cutting through this.
The first installment is titled ‘The Basics’, where we will introduce the history of die-cutting and the main categories of machinery.
The History of Die-Cutting
The development of mechanical paper die-cutting in Japan occurred after the Meiji period. With the diversification of consumption due to the Industrial Revolution, there was an increased demand for paper boxes that could be produced en masse at a low cost. To meet these demands, the printing industry expanded significantly. Consequently, the die-cutting industry, which processes these printed materials, also developed.
During the pre-war and post-war periods, the publishing industry flourished, and many publications were issued with supplements as part of sales competition. A wide variety of paper supplements were created, ranging from simple masks to complex paper model kits. Die-cutting significantly blossomed in fields beyond just box production.
As printed materials became even more diversified, the need for die-cutting expanded beyond publications to include various commercial printed media.
However, the printing and processing industry, which had been growing smoothly from the Meiji period through the 2000s, has been on a declining trend in recent years. This decline is due to the rise of soft packaging materials and PET materials in the case of boxes, and the decreased demand for publications and commercial printed materials due to the spread of the internet. Because supply capacity continued to expand to meet demand until the late ’90s, there has been an imbalance, resulting in a chronic state of excess supply capacity. As a result, the capabilities of die-cutting machinery and the cost per processing have remained almost unchanged over the past two to three decades.
However, the role of paper itself has evolved over time. Not only as a medium for information, but the flexibility to process the medium itself in ways that IT cannot has been increasingly recognized as an advantage. Therefore, the demand for die-cutting itself is unlikely to disappear in the future.
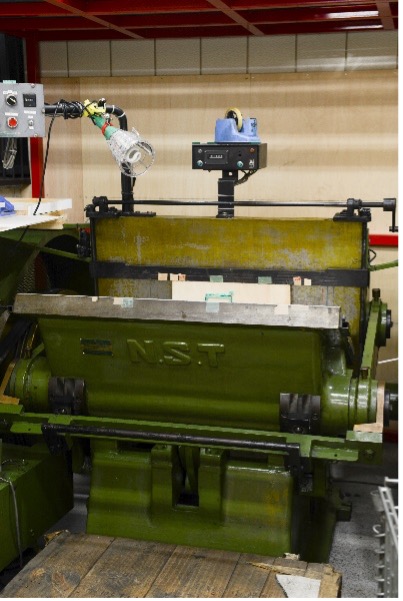
Our company’s inception and the first projects we undertook
Our company was established in 1957, coinciding with the emergence of children’s magazines as a genre. We began our business by handling the processing of supplements for these magazines. At that time, magazine supplements often involved quite elaborate paper crafts, and we still have samples in our office, such as the actual ‘Battleship Mikasa Assembly Kit’ that was a supplement in a children’s magazine from that era.
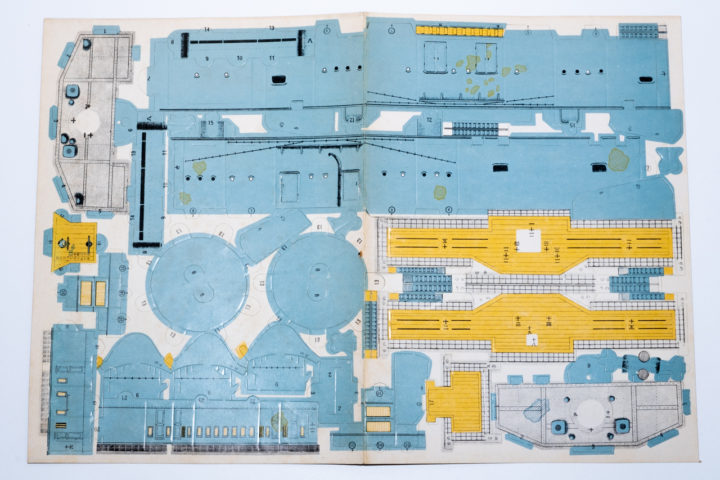
Types of Die-Cutting Machines
Die-cutting machines used in the process can be broadly classified into four types, each selected based on the type of paper being processed and the specifications required.
Here, we will briefly introduce the four types of mechanisms, their applications, and features. It’s worth noting that the names of these machine types may vary by region, and there are also colloquial terms within the industry, which can make it difficult for those outside the industry to understand.
Platen Die-Cutting Machine
The term refers to die-cutting machines represented by machines such as the Victoria Die-Cutter (Vic), the Thomson Die-Cutter (Laydown), and the Automatic Flatbed Die-Cutter (Auton). These machines can process a wide range of paper sizes and are capable of producing large quantities with stable quality. Because they operate on a flat surface, a significant amount of force is required, making the machines large. ‘Platen’ implies the application of flat pressure, so all flat press die-cutting machines are considered platen die-cutters. However, within the industry, ‘platen’ generally refers to Heidelberg’s platen printing presses.
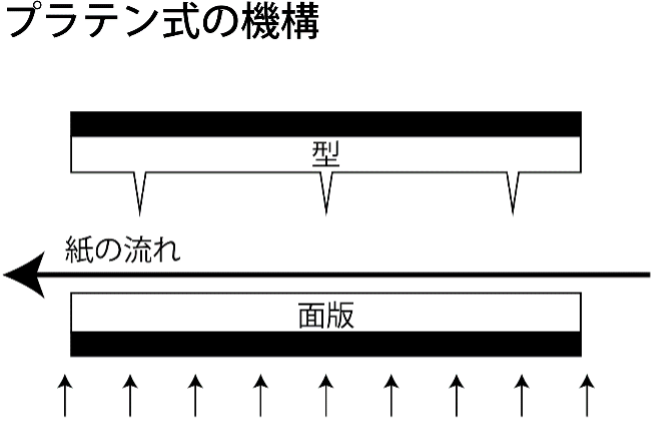
Cylinder Die-Cutting Machine
The cylinder die-cutting machine uses a cylindrical pressure roller (cylinder) for processing. The cylinder die-cutter by Heidelberg is the most famous machine employing this mechanism. Although the production of these machines has ended, many companies still use machines made over 40 years ago. They are particularly adept at cutting thin paper and are characterized by their high precision in alignment. In the die-cutting industry, ‘Heidel’ refers to the cylinder die-cutting machine.
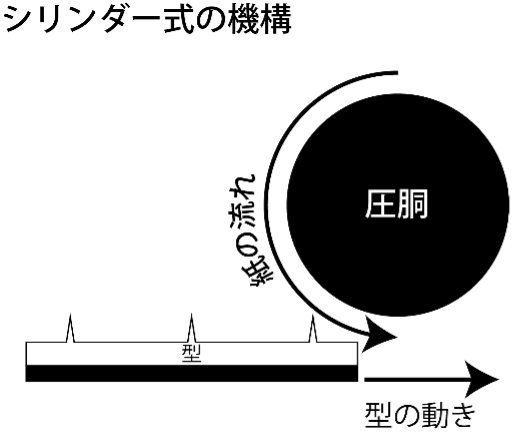
Rotary Die-Cutting Machine
Similar to the cylinder die-cutting machine, it utilizes a cylindrical pressure roller, but the difference is that the die itself is also cylindrical. It is often used for die-cutting seals with etched dies and processing thin paper. Etched dies are made of thin metal, which can easily be wrapped around a cylinder. For large machines, wooden dies are assembled for die-cutting cardboard. Since the paper does not need to be stopped at the die-cutting section, it allows for high-speed mass production.
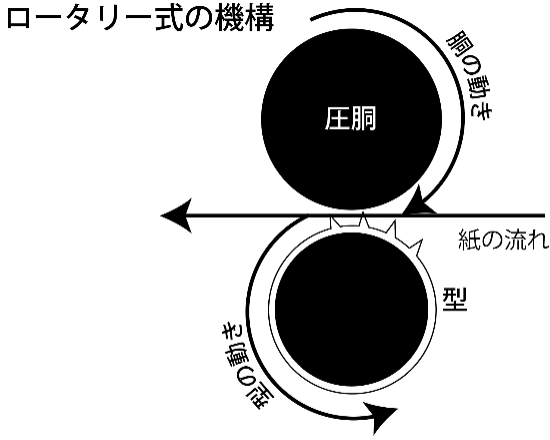
Push-Through Machine
Refers to punching machines such as ‘Bush’ and ‘Aisel’, which process in a ‘push-through’ manner. Although the processing speed is slow, it can punch hundreds of sheets of paper at once, allowing for mass production. It is used for die-cutting items such as notepads, various types of cards, playing cards, and thick post-it notes.
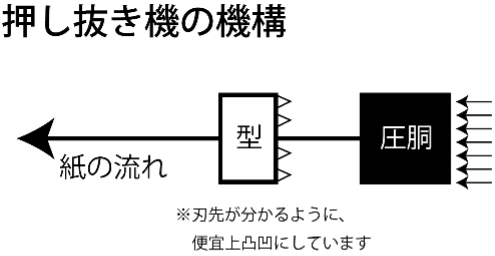
Our company uses a platen die-cutting machine.
Now that we have introduced the four types of die-cutting machines, our company possesses four automatic flatbed die-cutting machines, which are a type of platen die-cutter. We can handle sizes from A3 to double A size. The range of products that can be made through die-cutting is very wide, extending beyond magazine supplements to include restaurant menus, cork coasters, postcard perforations, puzzle die-cutting, and file tab making, among others. Essentially, if it can fit in the machine, we can probably die-cut it.
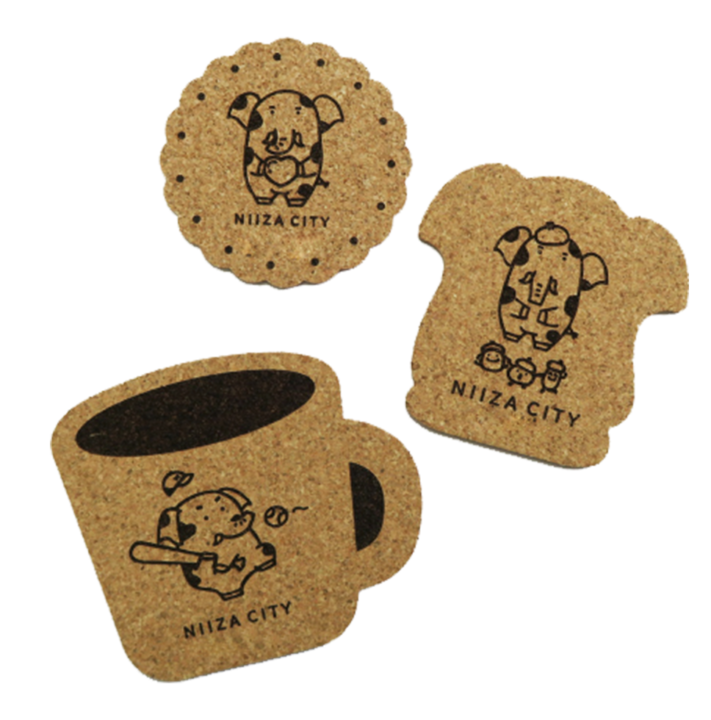
This time, we introduced the history of die-cutting and the classification of machines.
Next time, we’ll cover the Automatic Flatbed Die-Cutting Machine (Auton). Stay tuned!